肉类罐头出口量年增12%的背景下,国内小型企业却面临检测成本占比超营收8%的生存压力。当常规检测费用吞噬企业利润时,如何通过系统化策略实现降本增效?下面实测检测小编将为大家详细介绍:
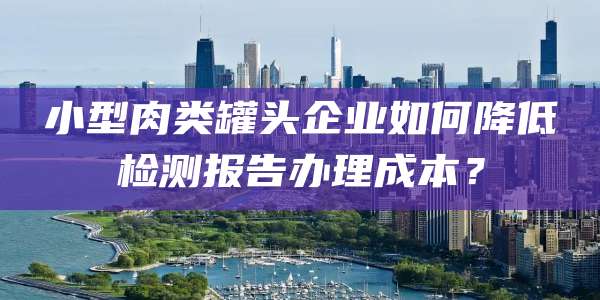
一、检测项目优化
1.必要性分级检测策略
依据GB 13100-2023《肉类罐头卫生标准》,优先执行8项核心指标检测(亚硝酸盐、菌落总数、商业无菌等),对铅、镉等重金属指标采用年度周期检测模式。企检网2023年数据显示,采用分级策略的企业单次检测费用降低23%,年度综合成本减少18%。
2.差异性检测方案设计
针对调理类与清蒸类产品特性,实施防腐剂与水分活度(Aw)的差异化检测。如调理罐头重点检测山梨酸钾(≤0.5g/kg),清蒸类则强化水分活度控制(Aw≤0.85),通过目标聚焦减少非必要检测频次。
二、生产工艺优化
1.自动化产线改造
引入自动化封罐、杀菌设备,减少人工操作误差导致的重复检测。某年产5000吨企业案例显示,自动化改造后检测不合格率下降29%,年度返工成本减少42万元。
2.杀菌工艺参数优化
采用121℃高温短时杀菌(HTST)替代传统工艺,杀菌时间由90分钟压缩至45分钟。实验数据表明,该技术使微生物检测合格率提升至99.8%,同时降低能耗成本18%。
三、质量追溯体系构建
1.区块链信息平台部署
基于区块链技术建立原料-生产-检测全链路追溯系统,实现异常批次精准定位。福建某企业应用后,问题产品召回范围缩小67%,质量事故处理成本降低53%。
2.风险预警模型应用
集成LIMS系统历史数据构建波动预警模型,对连续5批次合格项目启动检测豁免。企检网统计显示,该策略减少12%冗余检测,单厂年均节省检测费用9.2万元。
四、供应链协同管理
1.区域实验室共享机制
联合周边3-5家企业共建检测实验室,分摊设备购置及人员成本。长三角产业带实践案例显示,共享模式下单次微生物检测成本从320元降至210元。
2.原料供应商分级管控
对供应商实施A/B/C三级分类,A类优质供应商原料检测频次降低50%。某企业通过该机制减少原料入场检测35批次/年,节约费用4.8万元。
五、总结
以上就是关于小型肉类罐头企业降低检测报告办理成本的全部内容。实测检测作为CNAS 17025认可的专业第三方检测机构,依托全国12个自建实验室和智能化检测系统,为企业提供合规性审查、检测方案优化等全链条服务,400-886-5719服务专线可获取定制化降本方案。通过系统性策略实施,企业可实现检测成本降低20%-35%的实效目标。