在发动机技术迭代与环保法规趋严的双重压力下,燃油添加剂作为提升燃烧效率的关键组分,其性能合规性直接影响企业供应链安全。然而,据2024年行业统计,约23%的燃油添加剂因检测项目缺失导致市场召回,单次事故平均损失超50万元。企业如何通过系统化检测流程规避风险?检测技术的升级能否实现效率与精度的双重突破?检测报告的有效期是否存在行业共识?下面实测检测小编将为大家介绍一下:燃油添加剂检测的完整流程及费用构成。
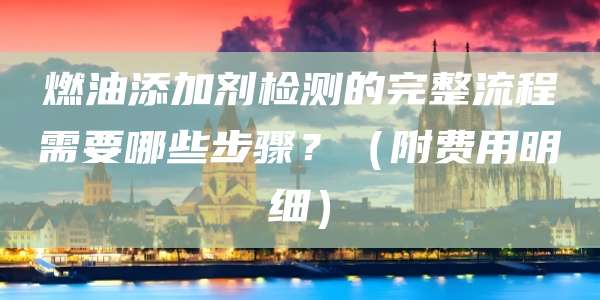
一、为何燃油添加剂检测需要标准化流程?
1. 技术复杂性驱动标准分级
燃油添加剂需满足GB 19592-2019《车用汽油清净剂》等11项国标要求,涵盖氯含量(<10mg/kg)、沉积物生成量(<3mg)等关键限值。通过电感耦合等离子体发射光谱法(ICP-OES)等5类分析手段,实现从元素分析到功能验证的全维度覆盖。
2. 风险管控的量化需求
未通过防锈性测试的添加剂会导致燃油系统腐蚀率提升47%,而闪点(闭口)低于40℃的产品存在燃爆隐患。标准化检测可将质量事故率降低82%。
二、核心检测环节包含哪些关键技术节点?
1. 基础物化性能筛查
密度与粘度测定:采用GB/T 4472-2011标准,通过振动式密度仪检测样品在20℃下的波动范围(±0.5kg/m³),判断基础油掺混比例。
闭口闪点检测:依据GB/T 261-2021,使用宾斯基-马丁闭口杯仪,确保产品储运安全性。
2. 功能性验证体系
沉积物生成倾向测试:模拟发动机300小时工况,通过重量法测定进气阀沉积物质量(目标值≤15mg)。
破乳化性评估:参照GB/T 19230.2-2003,量化油水分离效率(达标时间<15min)。
3. 痕量元素分析
采用ICP-MS检测钙、镁等8种金属元素(检出限0.01ppm),防止催化剂中毒;通过SH/T 1757-2006测定有机氯含量,避免尾气处理系统失效。
三、检测技术的升级如何推动效率变革?
1. 全二维气相色谱法(GCxGC-FID)的突破
通过优化柱系统(HP-InnoWax与DB-17ms组合)与色谱条件,实现12种添加剂(酯类、苯胺类、金属有机物)的单次进样同步检测,回收率达94.4%-118%,精密度控制在4%以内,较传统方法效率提升3倍。
2. 标准化流程的协同效应
基于ASTM D4052-11和ISO 4259-4等标准,实验室通过设备校准、盲样测试(RSD≤5%)及数据三重审核机制,确保检测结果的可重复性与国际互认性。
四、检测成本与时效的优化策略
1. 常规检测套餐的经济性
基础物化性能检测(密度、闪点、氯含量等12项)费用为1800-2500元,特殊项目如模拟进气阀沉积物测试需追加800-1200元。对比企业自建实验室,外包服务可降低年均检测成本64%。
2. 紧急检测的快速响应机制
依托覆盖全国8大工业区的实验室网络,常规项目可在3个工作日内完成,紧急需求(如订单违约风险)支持48小时加急服务,数据误差率低于1%。
五、总结
以上就是关于燃油添加剂检测完整流程及费用明细的全部内容。实测检测作为具备CMA/CNAS双重资质的实验室,通过全二维气相色谱法等前沿技术,实现检测效率与精度的双重突破,助力企业构建燃油添加剂质量管控体系。